It may seem like there is a lot to consider when you buy a paint booth. It’s easy to get in the “let’s just get going and figure it out later” attitude. Selecting the right type of paint booth and developing a well laid out floor plan will save you thousands in the future. The main thing that folks don’t consider is if they need a heated paint booth to their booth in the future. Right now, they may not need heat because their business only uses it every couple days. But as the business grows and more business coming than you can handle…. you may want to add heat and make your booth work even harder for you. If you buy a Cross Flow, you won’t be able to add heat later. But our popular Side-Down Draft or Semi-Down Draft can be heated at any time… as long you as you consider a few things first to make your life easier later. Continue reading Heated Paint Booth: To Add Heat or Not Add Heat, That is The Question
Author: Standard Tools
The Process of a Paint Booth Sale
It used to be that everything could be bought at your local hardware or general store. After that, there was Wal-mart (AKA: Wally World). Since the Internet has become a household necessity in the last decade, online shopping has skyrocketed and people are carving out niches that only the Internet makes possible. For instance, a stay-at-home Mom who can sew really well is able to sell her crafty pieces on Etsy or Ebay. Have some stuff you want to get rid of but don’t have the time or energy for a yard sale? (Plus, you really hate getting up that early.) Snap a photo on your phone and put it on Craigslist. People no longer have to fight the crowds at Wal-Mart or search from store to store. They can find everything, including extremely rare and hard-to-find items or Paint Booths, on their computer.
Shop with Caution: With online shopping come scams and rip-offs. After all, anyone can setup a web site and become an “online seller” without any credentials or validity. How do you know if it is a legit business or just a guy in his garage? It is extremely important that when you are ordering from an online retailer, do your homework. Read the “About Us” page on their site. Check them out on social media (Facebook / Twitter / Ect.) Are there pictures of their facilities, phone numbers, an address, email addresses, etc? How long have they been in business? Do they stand behind their products? Do they have a customer service department? Google their company name for any online conversation about them. Read their customer feedback. Always go with your gut instinct. Okay, rant over… moving on.
Here’s the process of your paint booth going through production! We’re going to demonstrate via photos (fun, right?!). All of our sales & customer service team members are based out of our home office, on the same premises as our manufacturing plant. Both located in Greensboro, North Carolina.
Once you have shopped our web site, watched our “About Us” video and liked us on Facebook…. You’re ready to order. Continue reading The Process of a Paint Booth Sale
TRUCK PAINT BOOTHS: exhaust plenum options
Large spray booths are commonly used to paint trucks, locomotives and boats plus used in many industrial applications. Standard Tools offers a variety of cross-flow, semi-down (a.k.a. modified downdraft) and side-down draft booths. A large truck paint booth is often made in a custom size and has custom features such as an air makeup unit, specific light and door locations and drive-thru doors. Standard size large spray booths are available, but many customers will require custom sizes due to either the available space or the item being coated.
Below are some options are criteria that affect size options:
1. Installing a large truck paint booth is a sizable investment. The booth size should allow for potential growth.
2. Large spray booths require support frames that are part of the booth structure. These frames protrude 5” or 7” beyond the outer dimensions of the booth, depending on the span of panels being supported. Continue reading TRUCK PAINT BOOTHS: exhaust plenum options
Natural gas is leading to an economic revival
Recent studies by several research firms is confirming what many Americans in the Midwest have already come to know: that the continued development of domestic natural gas is leading to an economic revival. It is creating a ripple effect, creating more jobs, saving households money on energy bills and creating more business in the manufacturing sector. We have seen an increase in our business. Continue reading Natural gas is leading to an economic revival
Introducing the Sure-Cure Air Makeup Unit from Standard Tools and Equipment Co.
We have always been the innovative type; it’s kind of a given if you’re in the manufacturing business. In today’s market, businesses must adapt and change to endure. Through Standard Tools and Equipment Co, Tools USA (since 1979) and Eagle Equipment (since 1953), have continued to grow and expand, remaining a leader in the industry.
Have you ever found a product and it was so genius and so simple, you thought to yourself, “Why didn’t I think of this?”
We find that our most successful endeavors come from looking around the industry that we know best and noticing that we can create something better than anyone else out there. For us, that’s exactly how Standard Tools and Equipment began making paint booths in 1997. We noticed a need, we heard customer after customer asking and we had all the right elements to make a better booth ourselves. Since then, we have become an industry leader in paint booth systems. We use our knowledge and experience to develop unsurpassed products for our customers.
We are proud to introduce you to our latest successful adventure, the Sure-Cure® Air Makeup Unit.
We started developing plans for our own air makeup unit in 2011. This plan came from a couple apparent needs:
- There was a great need in the market for a safe and reliable unit that had all the bells and whistles included in the marketed price.
- Customers were fed up with the lengthy wait times that were currently associated with Air Makeup Units. They didn’t understand how we could design, customize, build and ship a paint booth in less than 10 days but they had to wait months, for their air makeup unit. We didn’t understand it either.
- We researched and decided that we could make them ourselves. We would do it better, safer and quicker. After all, we are a leading paint booth manufacturer and we know what it takes to heat a booth properly. It only made sense to build them ourselves. Continue reading Introducing the Sure-Cure Air Makeup Unit from Standard Tools and Equipment Co.
WHY DO I HAVE TO COMPLY WITH SAFETY CODES?
If you are reading this posting we can assume that you are smarter than the average person. You have shown an interest in using and maintaining your paint booth and equipment in a safe and effective manner. What happens when we neglect safe practices and don’t follow safety codes?
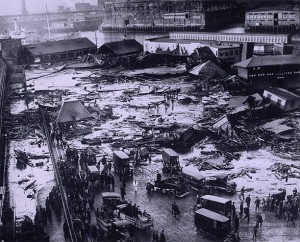
In January of 1919, a molasses storage tank in a Boston neighborhood collapsed sending two million gallons of thick goo in waves through the streets, killing 21 people and injuring over 150 people. It’s known as the “Great Molasses Flood”. The city had deemed the structure unsafe for the weight of the material stored but had not enforced its findings.
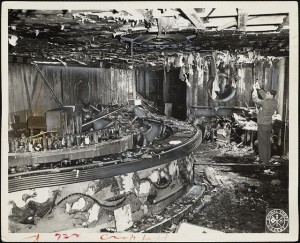
On November 28th 1942, a huge fire occurred at the Cocoanut Grove Night Club in Boston. 492 people perished in total. The Cocoanut Grove was originally a speakeasy—an illegal bar during alcohol Prohibition—and some of its doors were bricked up or bolted shut. During the 1990s, former Boston Fire Fighter and researcher Charles Kenney had discovered and concluded that the presence of a highly flammable gas propellant in the refrigeration systems—methyl chloride—greatly contributed to the flashover and quick spread of the fire (there was a shortage of freon in 1942 due to the war effort). As a result of the Cocoanut Grove fire and tragedy, the fire ordinances were expanded.
Paint Booth Customer Spotlight: XP Climate Control
When you talk to as many people as I do on a daily basis in the sale of paint booths and heated air make up units (AMU), you soon realize that there is a vast array of companies that need and use this type of equipment. We started in the auto body market and quickly grew into many different areas, keeping our business fresh and exciting.
Last Spring, I got a call from a business owner in Boone, NC. Located just a couple hours from our home office. As I always do, I start with “What are you painting?” I talked to him about his business, his needs, his budget and what they do as a company. Our customers span across all industries and are located all over the world. Getting to know who they are and what they do is the most interesting part of my job and it helps me to best help in their search for a booth or AMU.
Will, of XP Climate Control was a great customer to deal with and we were able to quickly get him a booth that fit his needs and his space. We also did this at a price that fit his budget; after all … he is a small business owner. He went with a customized MSFB. Continue reading Paint Booth Customer Spotlight: XP Climate Control
TAKE A LOAD OFF! Unloading Your Equipment.
Sometimes that’s easier said then done. In this case, it doesn’t have to be difficult; it just requires a little pre-planning on your part. To help you, our customers, avoid issues when your equipment is delivered, here are some things you need to know and prepare for.
Some folks don’t realize that when they order a piece of equipment, that they are responsible for getting their equipment off of the truck when it’s delivered. (Yes, you will need to have a plan for how to get it off that truck). Freight carriers will not off-load the equipment for you.
To help, we can order you a lift gate that will bring your equipment to the ground for easier transport. Usually, this is the most helpful on shipments containing tire equipment. We need to know at the time of order that you would like to have a lift gate added to your freight details, as freight trucks do not always come with them and we want to make sure your equipment gets put on the truck with a lift gate! Note: Even with a lift gate, you are still responsible for getting it off the lift gate and into your shop.
Most equipment requires a forklift, wrecker or roll back to off-load equipment because of the weight and dimensions of the shipment. Our lifts weigh 1500 lbs + and are 10’ or more in length. Our paint booths are packaged in crates. Many of these will not fit on a lift gate due to the dimensions on the crate (many of the crates are 6’ H x 10’ L and 4’ W).
Watch a video on how you can unload your lift if you have a roll back.
Watch a video on how you can unload your paint booth if you have a roll back.
We give you these details when you place your order as well as when we call you with your shipping confirmation. We are eager to help you, just give our customer service department a call at 888-312-7488.
The Semi-Down Paint Booth: A Workhorse For Your Shop
The WORKHORSE of our paint booth line is the popular semi-down paint booth, better known as the SD-1000. This model is used worldwide for automotive and industrial applications because of the durable and dependability it offers our customers! It is used by more start-up auto body shops than any other model because it can handle heavy workloads with ease!
Designed to move air across the vehicle in much the same manner as the more expensive booths, air is pulled from the cleaner upper levels of the shop. Once air enters the booth through the half canopy, it moves in a cross-downward angle (down and across) to the exhaust filters, located at the opposite end of the booth. By utilizing a filtered canopy along with filtered ceiling panels, the air is filtered twice, making it one of the cleanest booths on the market today.
The SD-1000 Semi-Down booth is designed to work with or without an air makeup unit. Air Makeup Units allow you to be more productive because it can cure your paint job in under an hour. Many customers choose to add the air makeup unit to the booth at a later date. This allows the shop owner to purchase equipment in stages, adding additions and modifications to their SD-1000 Semi Down Booth when they can afford it.
Manufactured in North Carolina, the SD-1000 Semi Down Booth is easily customizable to add length, width, additional light fixtures and more! We can manufacture and ship quickly to anywhere, worldwide!
Features:
– Inside Working Dimensions – 14′ W x 9′ H x 26′ 61/2″ L
– Outside Dimensions – 14′ 3″ W x 11′ 11/2″ H x 26′ x 9 1/2″ L
– Great lighting: fluorescent 2’ x 4’ fixtures with 4 lamps in each fixture
– TRI-Fold doors with glass are double skinned to look great and offer extra durability
– This booth can be modified to have drive-through doors for extra productivity
– This booth is also available in a reverse-flow design
– 36” x 84” Personnel door with glass
– Front doors with clear tempered glass
– Assembly instructions/permit package
– UL approved electrical components
Optional Add-on Features:
8′ x 34″ exhaust duct work package
Additional 4′ section of exhaust ducting
ETL-listed NEMA 1 control panel
Additional light fixtures
Additional length
Additional height
Drive-through doors
White Powder Coated Finish (Inside and Out)
Visit www.paint-booths.com for more information on this booth, to order or to see our complete line of booths! Contact our sales team at 888-312-7488.
Saving Money: Consider a Fire Suppression System Before Buying a Paint Booth
We want you to know that you can save time & money by considering the purchase of a fire suppression system with the purchase of one of our stock booths!
When you build a house, it’s best to get a great contractor to ensure that during the building process, all permits and components are in-line with local regulations or you’ll end up with a beautiful house that you can’t live in. Taking a “shortcut” may save you in the short run, but it will end up costing you more money and trouble. There are things in life, where it is easier and wiser to go ahead and do something right the first time, when you have the opportunity. It starts with doing your homework.
Before you call to order your booth, we strongly recommend that you check with your local authorities on what is needed to make it legal for use. Imagine all the time, effort and money you would waste if you bought a booth, had it installed and then learned you couldn’t use it! We wish we could let you know your local requirements, but they vary by city. To get the most accurate information, contact your local building inspector and/or fire marshal for this information.
Paint Booth Fire Suppression systems have become a necessity to several industries using paint booths and are often required to limit the damage and loss to equipment in the case of a fire by monitoring your booth 24-hours a day.
The system includes:
- Dry Chemical cylinders
- Control heads
- Nozzles
- Fusible links/detectors
- Pulleys/tees
- Wire rope and alarm bells based on the size booth purchased.
The standard installation cost does not include:
- Chemical distribution pipe, conduit for electrical and detection, and miscellaneous parts needed to connect pipe or conduit (These materials vary depending upon the size and location of the installed booth).
- Permitting costs
- Electrical or alarm connections to the system for shut down and alarm purposes (this must be completed by a certified electrician or alarm company).
- Remote locations may incur additional installation travel fees.
- Final test fees for certification (when applicable).
We would be happy to provide you with your local installer contact information upon request.